
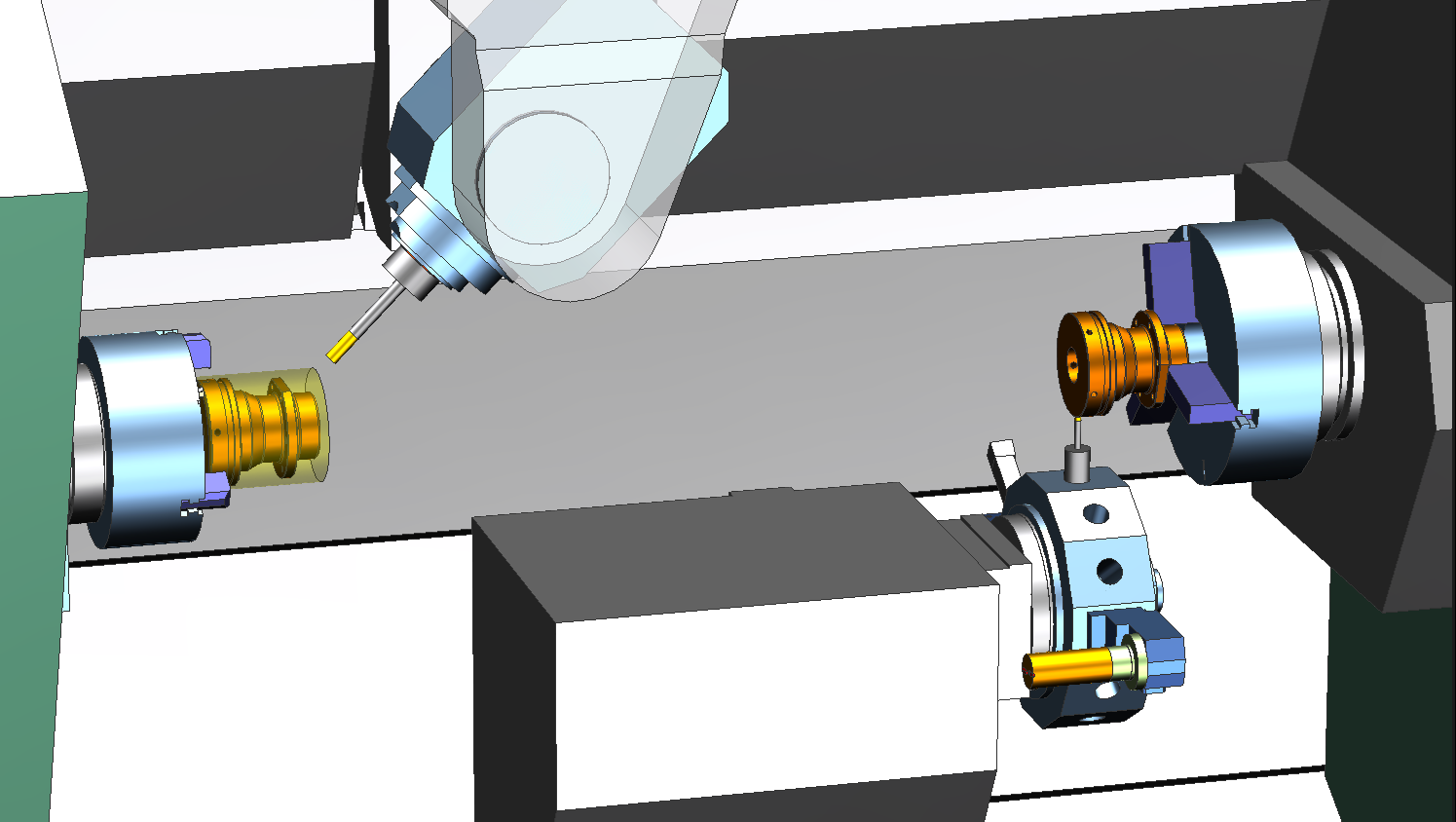
This paper presented the existence of the tool position with double contact points through analyzing different types of error distribution curves. An error distribution curve was used to describe the gap between a barrel cutter and a surface. The strip width of the tool position is larger than that of the tool position solved by the single-point offset method. It can be used to compute the tool position, at which the cutter can contact with the surface at two points. This paper presents a novel tool positioning method for flank milling with a barrel cutter. The numerical example illustrates the effectiveness of the proposed method. An algorithm based on the Differential Evolution algorithm is developed to solve this model. Thereafter, a multi-criteria tool path generation model is established, and it is converted into a single-objective optimization with the weighted sum method. Accordingly, the swept profile of the cutter at each cutter contact point is employed to evaluate the machining width naturally. The machined part geometry is the complement of the cutter’s swept envelope from the stock. tool shank and holder, are also detected. Local gouge between the tool flute surface and the blade to be machined is considered, and the collisions of the blisk with the non-cutting parts of the tool, i.e.

A method of generating collision-free and large-machining width flank milling paths with smooth axes movements for blisk machining with barrel cutters is proposed.
#Software for blisk machining software
However, the barrel cutters are more challenging for CAM software to generate paths. Therefore, barrel cutters are suitable for five-axis blisk machining. The optimized conical cutter can be tangent to the multi-constraints of the workpiece but do no interfer with them.Ī barrel cutter has a cutting segment with a large radius on its profile, and this arc segment allows the cutter to tilt away from the part surface, avoiding the collisions of the tool with the part. The results show that the proposed method can efficiently and accurately calculate the max size and tool orientation of the conical cutter simultaneously. Finally, the proposed method is verified by three simulation experiments and a comparison experiment. The solving algorithm is designed based on the 3D Medial Axis Transformation (3D MAT) theory. Fourthly, the mathematical model and solving algorithm for the max-size CSCS is given. Thirdly, the CSCS with special situations is discussed and the calculation method is proposed. Secondly, the concept of CSCS is proposed based on the deduced mathematical principle and the calculation method of the CSCS with the general situation is provided. Firstly, the mathematical principle of the conical cutter generated by a cylindrical cutter is deduced based on the motion envelope theory. The conical cutter generated by CSCS can reach a critical state with multi-constraints simultaneously.

With this concept, the complex multi-constraints of the workpiece can be transformed into several simple but precise geometric conditions to optimize the size and tool orientation of a conical cutter. In this paper, the concept of cutter size critical sphere (CSCS) is presented, which is a specified sphere and tangent to several geometric constraints of tool accessible regions.
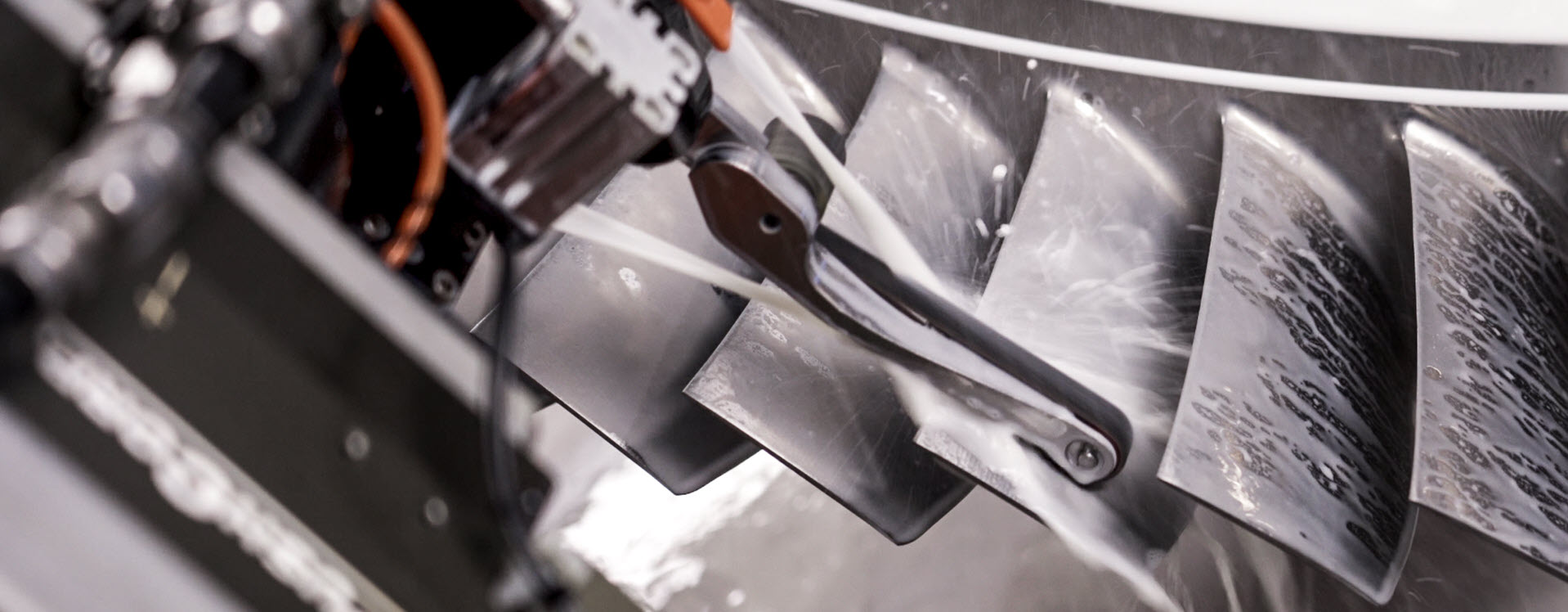
Increasing the cutter size to enhance its stiffness is of great significance for improving the machining efficiency and precision of deep and narrow channel parts. Therefore, this method can be directly applied in the CNC machining of blisk or centrifugal impeller. The numerical examples prove that a feasible barrel cutter with the higher productivity can be obtained by the proposed method in this paper. Finally, the tool shaft diameter is optimized to improve tool rigidity and avoid the global interferences between the tool shaft and the adjacent blades. Furthermore, in order to avoid the global interferences between the tool shaft and the blade in process, the center point of circular arc generatrix is adjusted. Meanwhile, the local gouges and kinematic constraints of the CNC machine tool are also taken into account. Then the optimal size of tool flute with a greater barrel radius is determined. The geometric properties and location of four types of barrel cutter are firstly introduced. In this paper, a new method is proposed to select an optimal barrel cutter in the interest of the high productivity in the CNC machining of blisk. Barrel cutters have been widely used in the flank milling of blisk.
